The first 212-foot-tall SLS core stage is on test stand B-2 at NASA’s Stennis Space Center in Mississippi, where it has completed a series of eight major tests known as Green Run. The tests included nearly 30 firsts: first loading of the propellant tanks; first flow through the propellant feed systems; first exposure of the stage to the vibrations and temperatures of launch; and ultimately, first firing of all four engines for more than eight minutes, just as they will during launch on the Artemis I uncrewed mission around the moon. This Green Run will help verify the SLS core stage design for the first rocket and all others to come.
Rocket to the Moon, Mars and Beyond
- NASA’s Space Launch System is the only rocket capable of carrying crew and large cargo to deep space in a single launch.
- Powered by the Boeing-built Core Stage, SLS successfully launched as part of the Artemis I Mission on November 16, 2022.
- Work has already begun on the Core Stages for Artemis II-V and the Exploration Upper Stage, the replacement for the Interim Cryogenic Propulsion Stage for Artemis IV and beyond.
Boeing people and products have powered giant leaps in human space exploration over the past six decades. Now, with the NASA Artemis program — named after Apollo’s twin sister — Boeing will be part of landing the first woman and first person of color on the Moon and the sustainable exploration of more of the lunar surface than ever before. What NASA and its commercial and international partners learn on and around the Moon will enable astronauts to take the next giant leap — all the way to Mars. NASA’s Space Launch System (SLS) is the only proven deep-space optimized, super-heavy lift rocket built to carry astronauts and cargo farther and faster than any rocket in history.
Boeing is the prime contractor for the design, development, test and production of the SLS core stage, upper stages and flight avionics suite. On November 16, 2022, the SLS rocket successfully launched as part of the Artemis I Mission, which served as an uncrewed test flight to validate the rocket components and systems in preparation for future crewed missions. Boeing is currently building the core stages for Artemis II, III, IV, and V, as well as the first Exploration Upper Stage, which will replace the Interim Cryogenic Propulsion Stage (ICPS) in future Artemis missions.
The Next Mission
SLS will launch a permanent human presence in deep space. Its flexibility and evolvability will support diverse exploration, science and security missions.
During the Artemis II mission, SLS will fly in the Block 1 configuration and launch the first crewed Orion spacecraft on a flight path around the Moon carrying the first female and person of color to lunar orbit!
Additional missions are planned with the SLS Block 1B configuration – equipped with the Exploration Upper Stage (EUS). The EUS will provide NASA with a stage fully capable of carrying humans, enabling deep space exploration with significant payload capabilities. It is expected to allow 40 percent more payload to the Moon compared to the SLS Block 1 configuration.
Boeing is producing flight hardware for Artemis II and beyond.
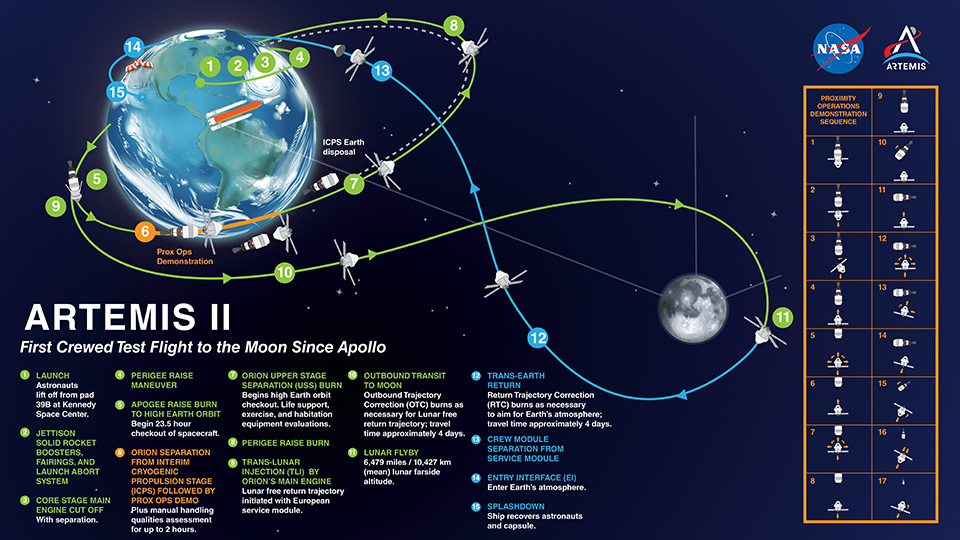
- B-2 Test Stand
- Test 1 Modal Test
- Test 2 Avionics
- Test 3 Fail-Safes
- Test 4 Propulsions
- Test 5 Thrust Vector Controls
- Test 6 Countdown
- Test 7 Wet Dress Rehearsal
- Test 8 Hot Fire
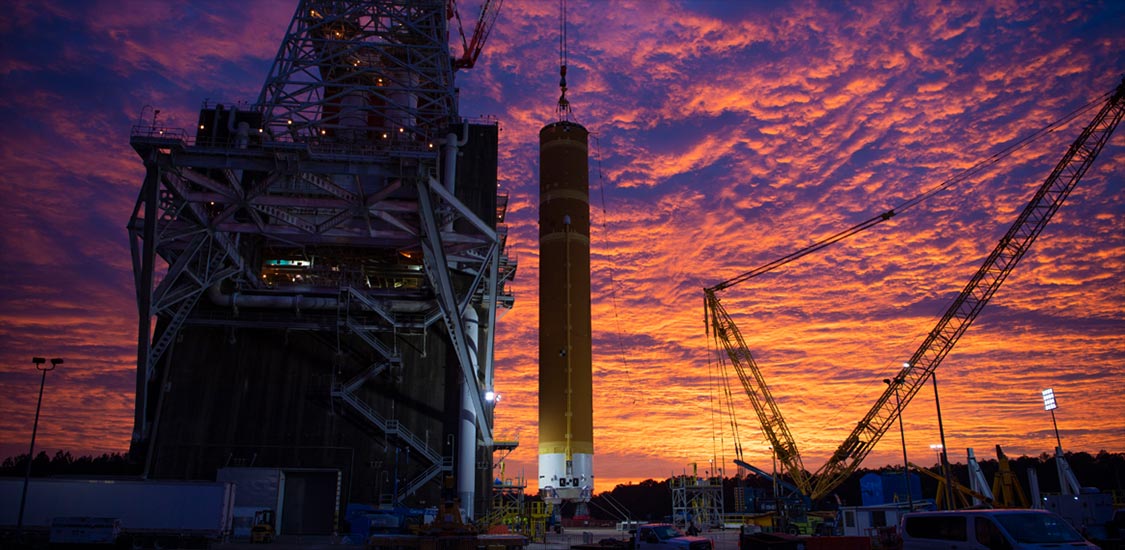
B-2 Test Stand
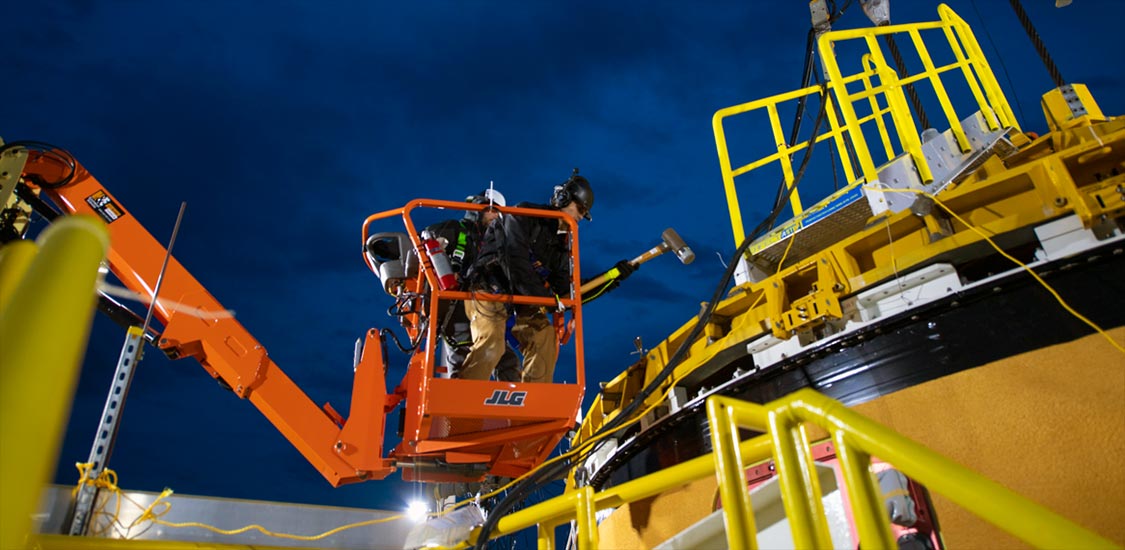
Test 1: Modal Test
The test used a series of actuators to shake the rocket at three different locations along the stage to mimic the stresses the stage will endure during launch and flight. Engineers also manually used an impulse hammer to test the spider crane, which holds the stage in place, to help establish a baseline for any impact the test stand or external hardware could have on test data. Test data will be used to verify structural vibration modes and flight control parameters for core stage design.
Completed | January 2020
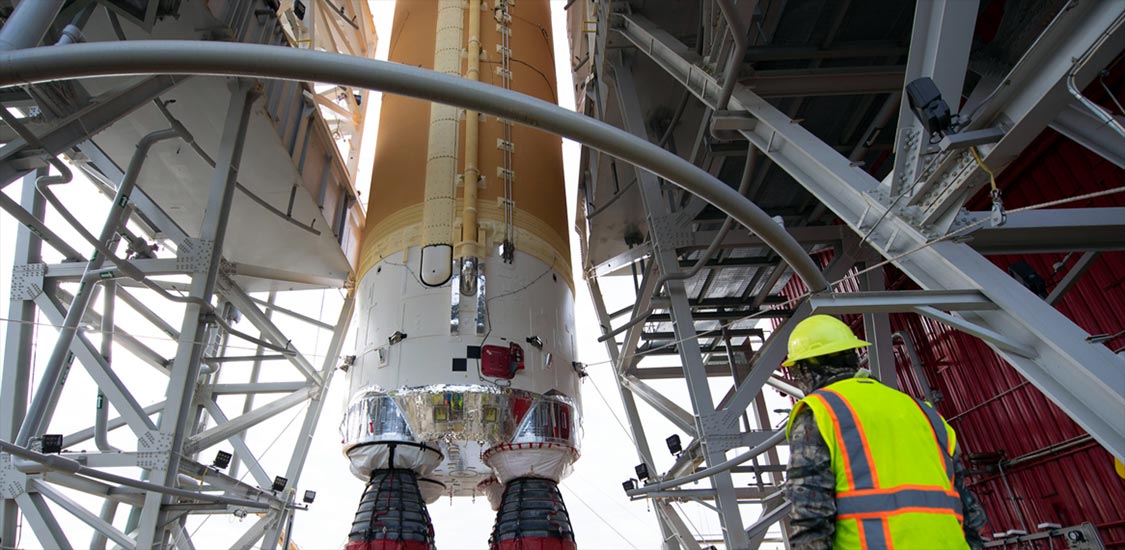
Test 2: Avionics
The rocket’s avionics, which are distributed throughout the stage, were turned on and checked out. This included the flight computers and electronics that control the rocket and also those that collect flight data and monitor the overall health of the core stage. The flight computers and avionics are located in the forward skirt, the top section of the core stage, with more avionics distributed in the core’s intertank and engine section.
Completed | June 2020
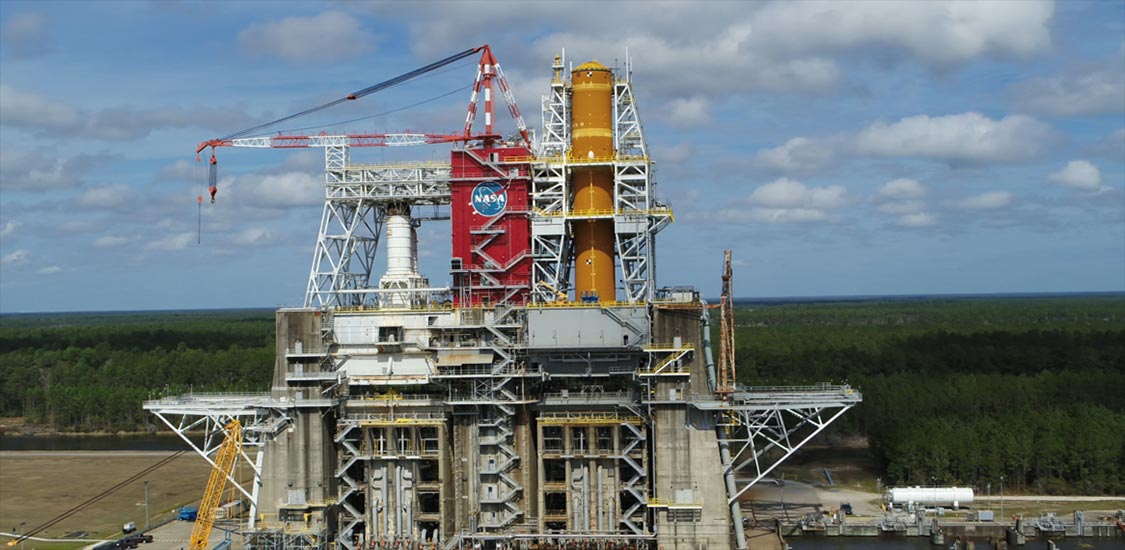
Test 3: Fail-Safes
Engineers checked all the safety systems that can automatically or manually shut down operations during hot fire. To do this, they simulated potential issues.
Completed | July 2020
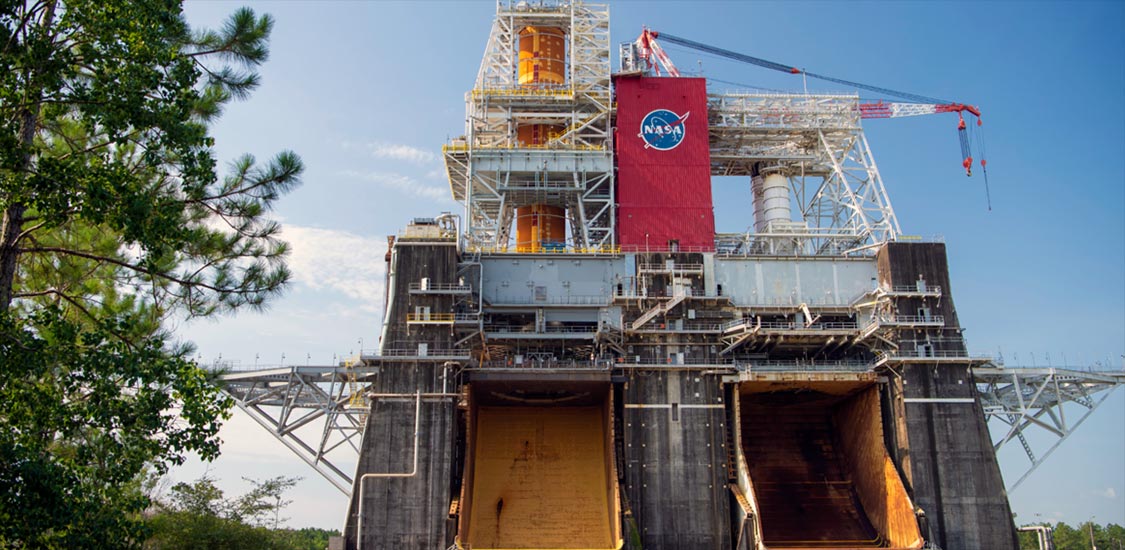
Test 4: Propulsion
This was the first test of each of the main core stage propulsion system components that connect to the engines. Command and control operations were verified, and the stage was checked for fluid or gas leaks.
Completed | August 2020
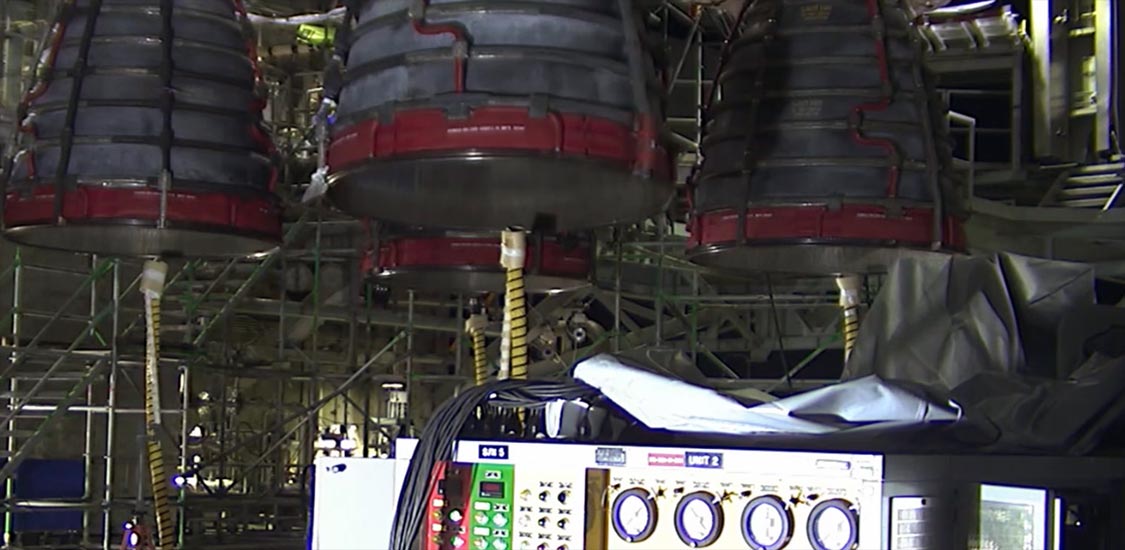
Test 5: Thrust Vector Controls
Engineers ensured that the thrust vector control (TVC) system could move the four RS-25 engines and checked all the related hydraulic systems. The engines, attached to the core stage, moved back and forth during a steering test. Engineers also fully verified the sequence of commands for ignition and engine cutoff.
Completed | September 2020
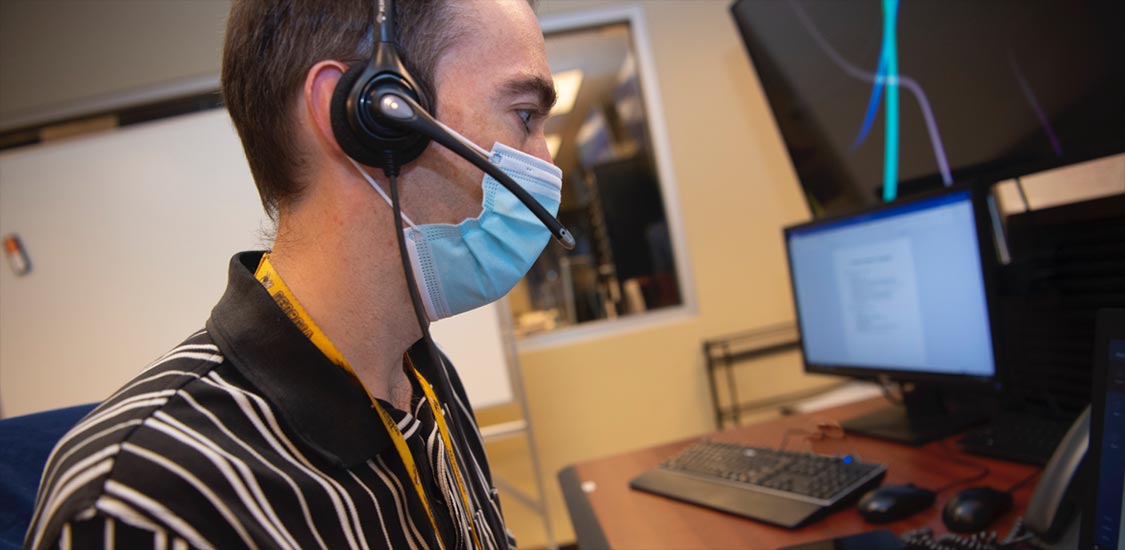
Test 6: Countdown
The simulated countdown rehearsed the launch countdown, including step-by-step fueling procedures. Core stage avionics were powered on, and propellant loading and pressurization were simulated. The test team validated the countdown timeline and sequence of events.
Completed | October 2020
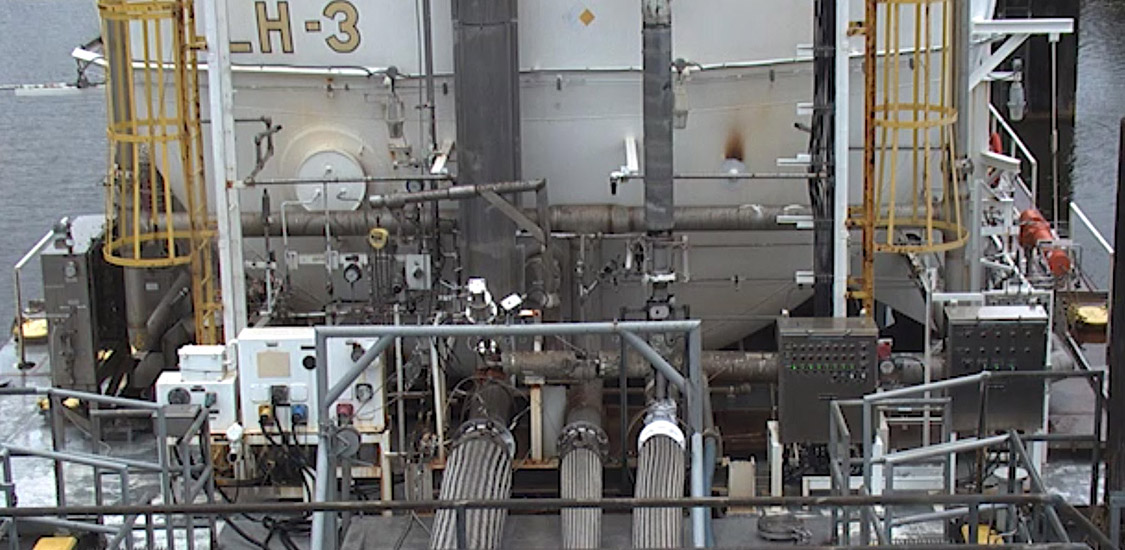
Test 7: Wet Dress Rehearsal
Engineers demonstrated loading, controlling and draining more than 700,000 gallons (2.6 million liters) of cryogenic propellants into the liquid oxygen and liquid hydrogen tanks and then returning the stage to a safe condition. Toward the end of the simulated terminal countdown, the test automatically stopped due to a valve closure being off by a fraction of a second. The team has corrected the timing, and additional analysis clears the way for hot fire.
Completed | January 2021
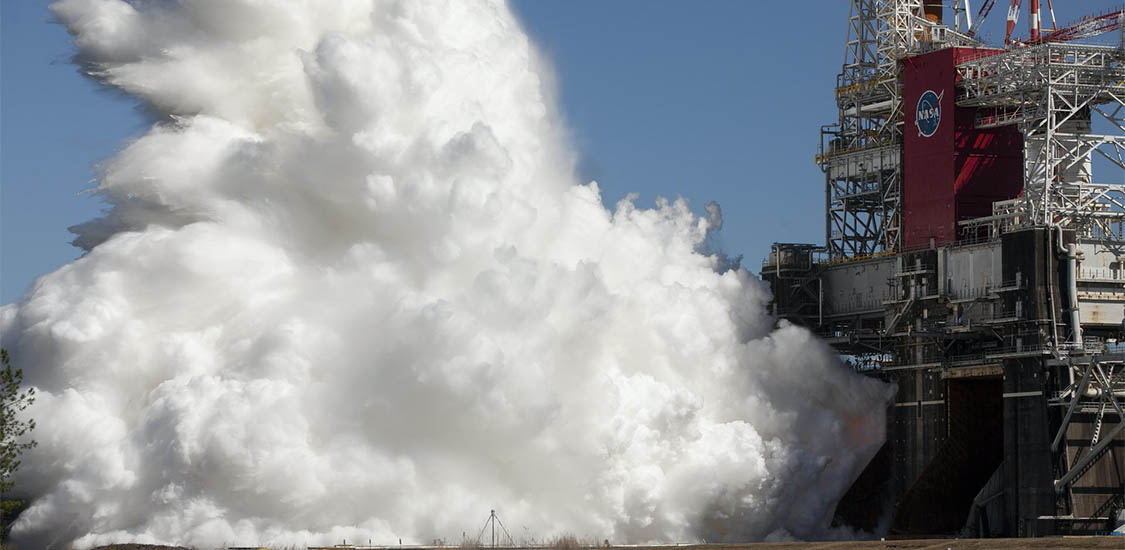
Test 8: Hot Fire
The core stage was turned on, loaded with supercooled propellants, and taken through a countdown including holds until the four RS-25 engines were fired for a full-duration, eight-minute burn in a simulation of launch and ascent. The engines generated 1.6 million pounds of thrust, the same as they will on the Kennedy Space Center launchpad at liftoff in 2021.
Completed | March 2021
Next, the team will review the data and refurbish the stage to prepare it for delivery to Kennedy. There, it will be joined with the rest of SLS to become an operational rocket on the road to launch.
Feature Stories
Space Launch System Gallery
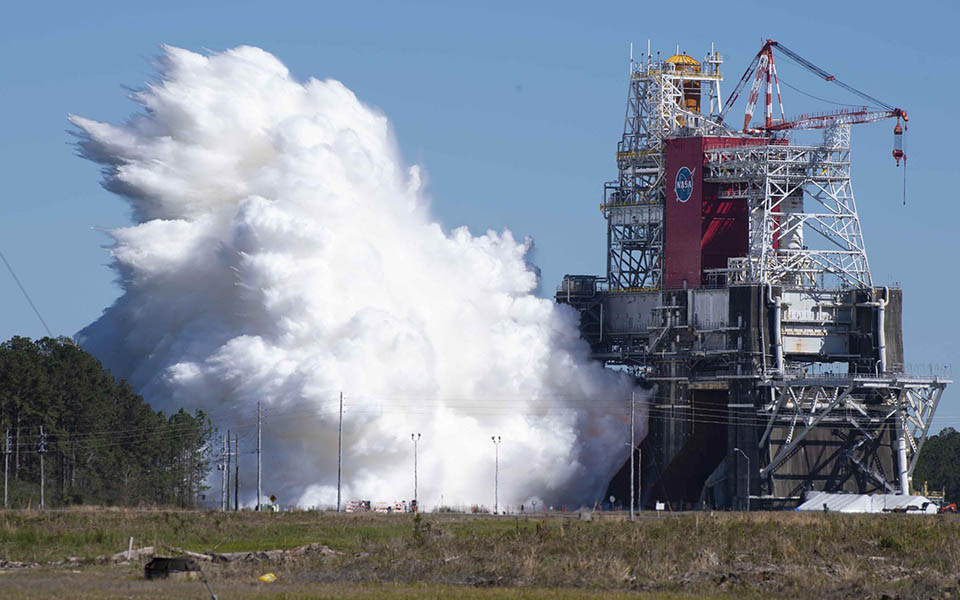
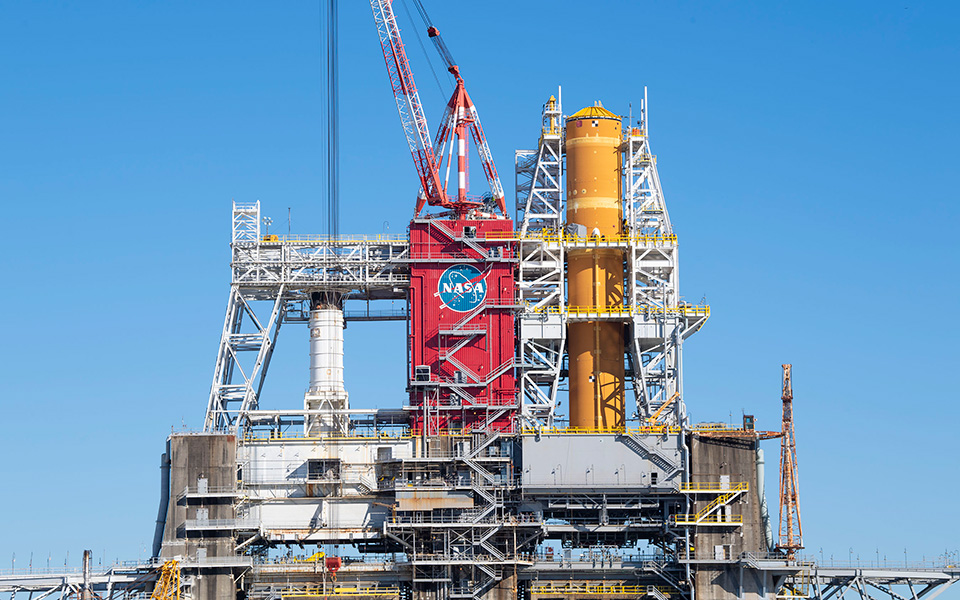
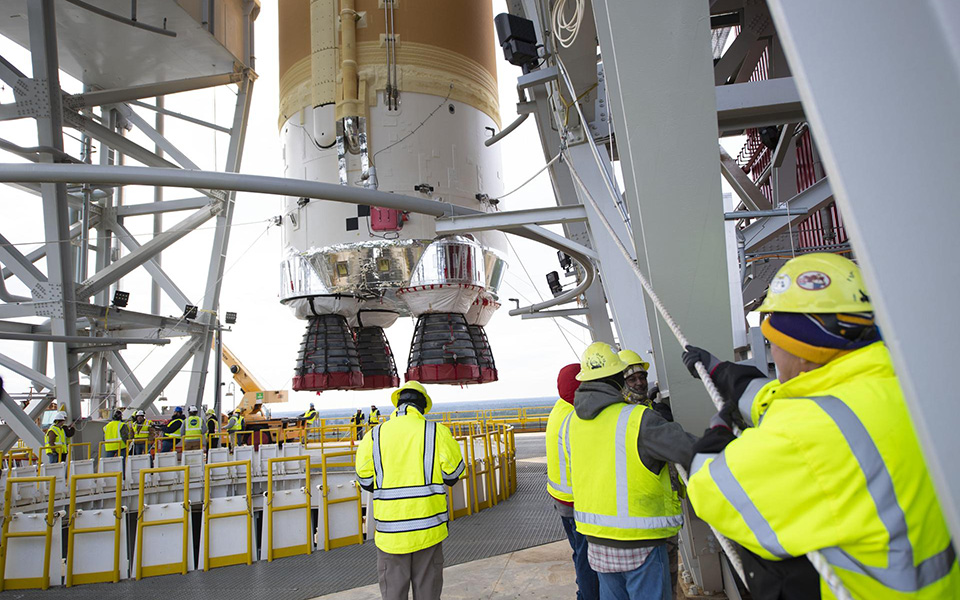
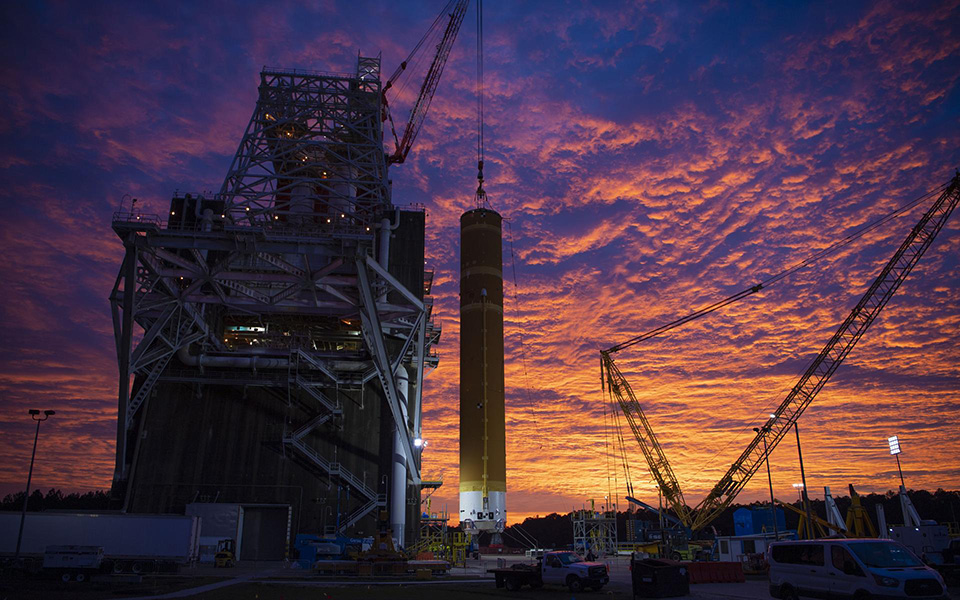
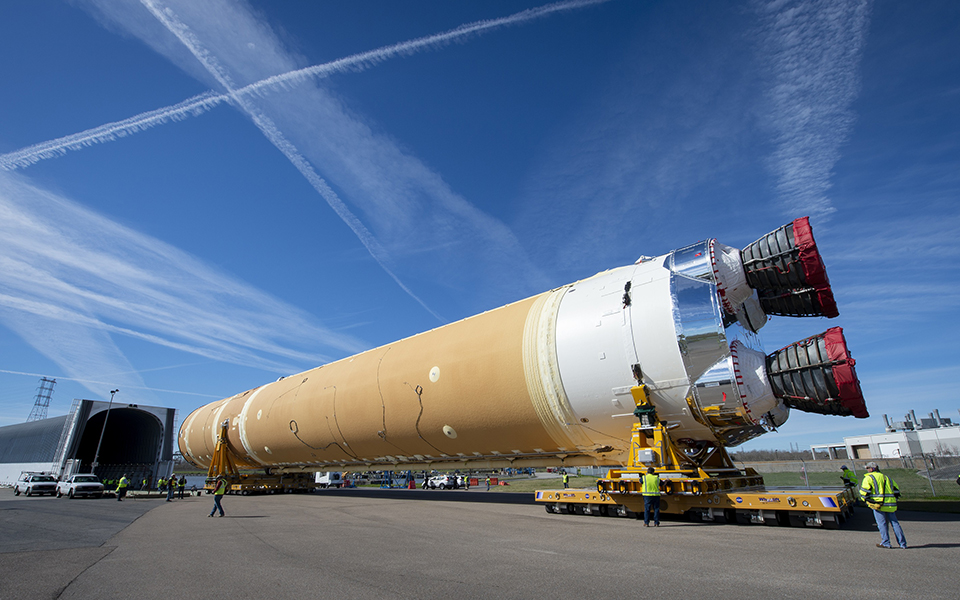
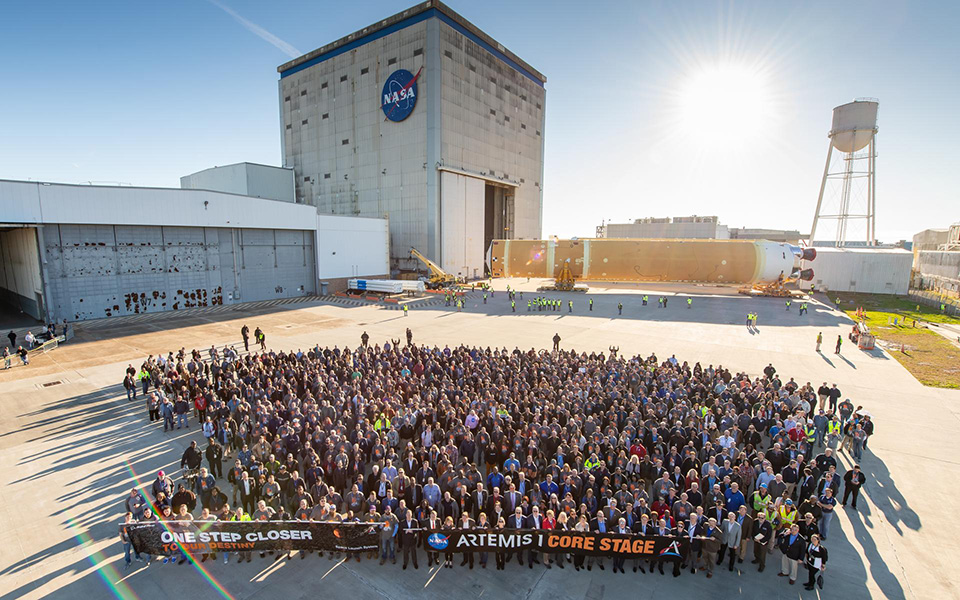
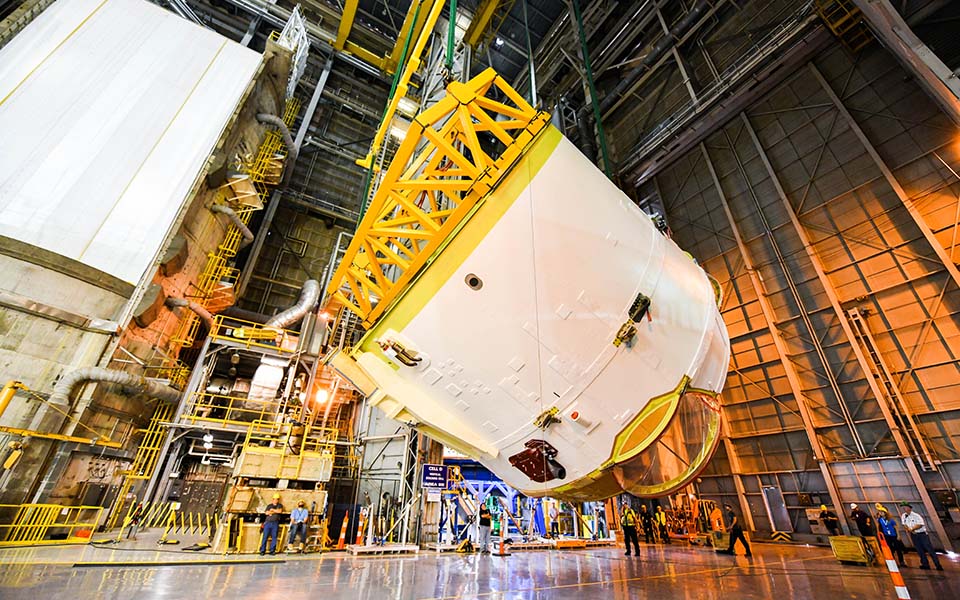
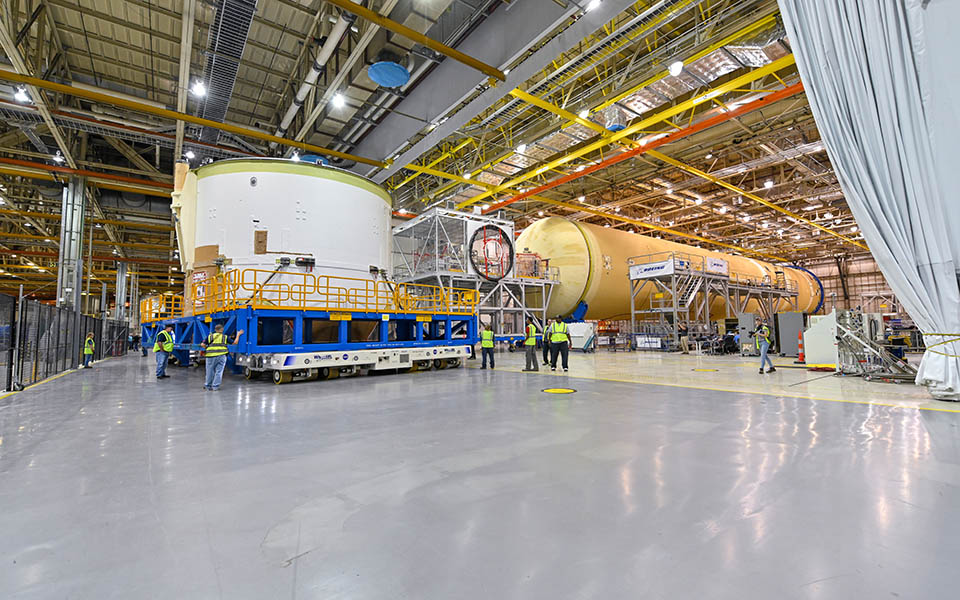
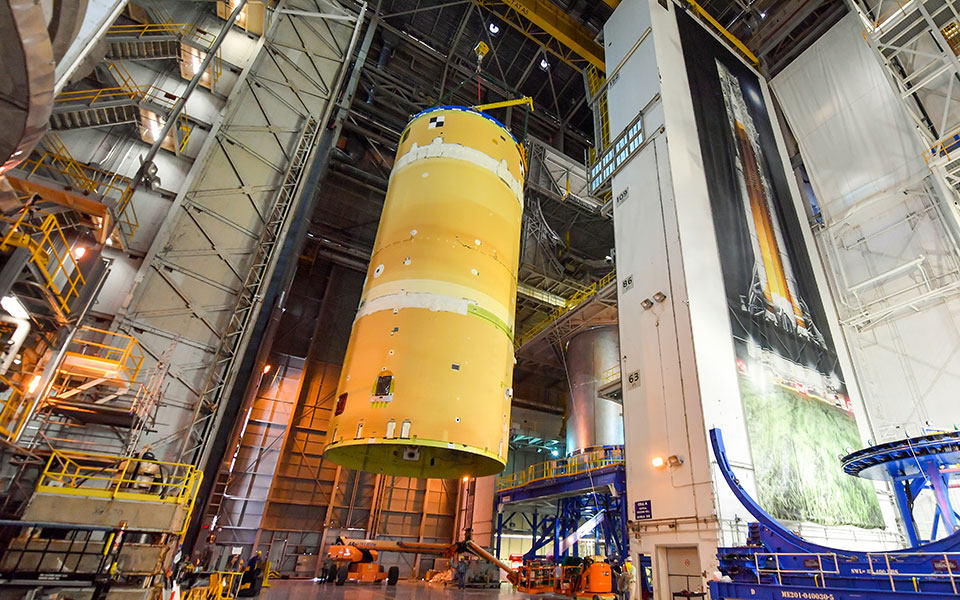
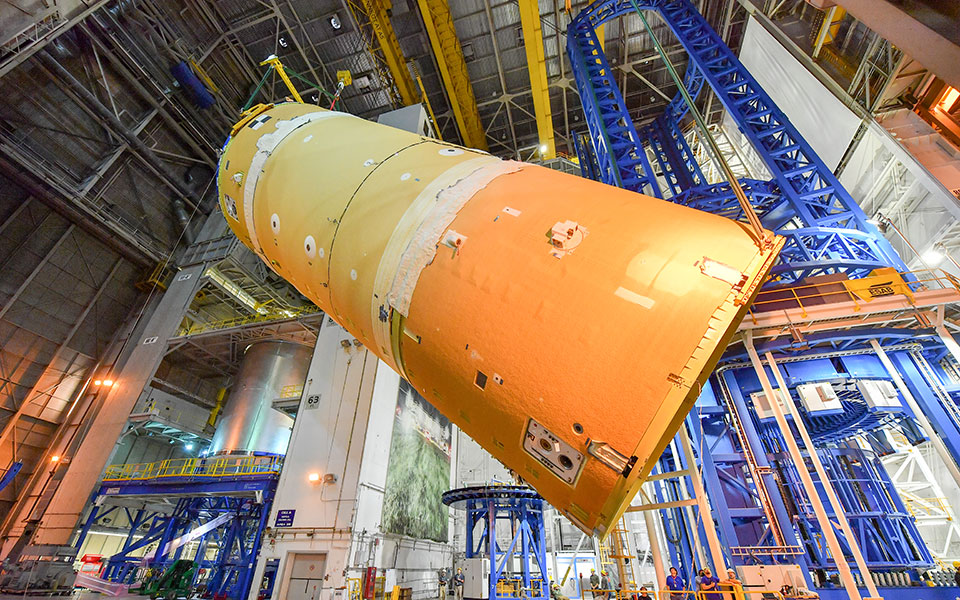
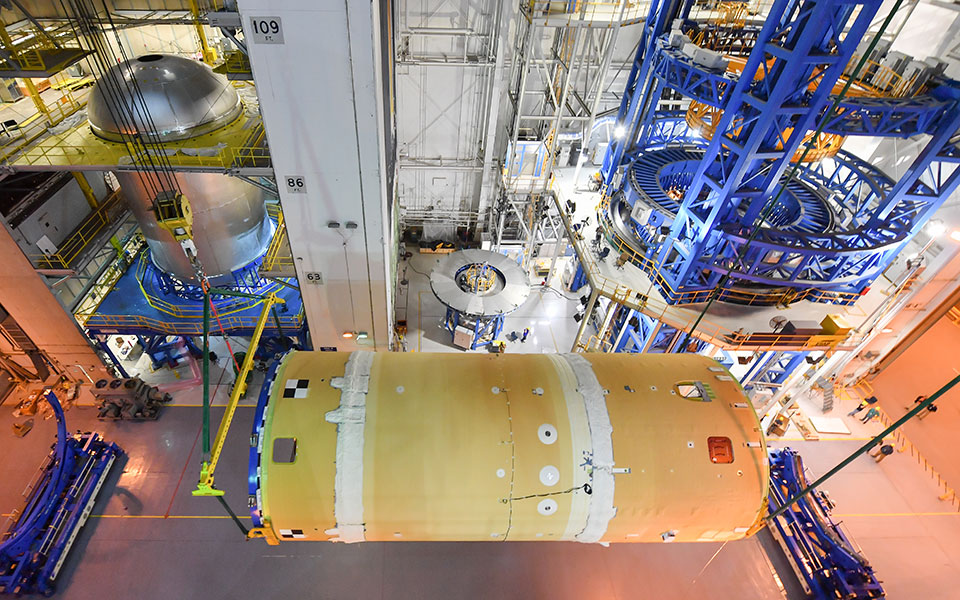
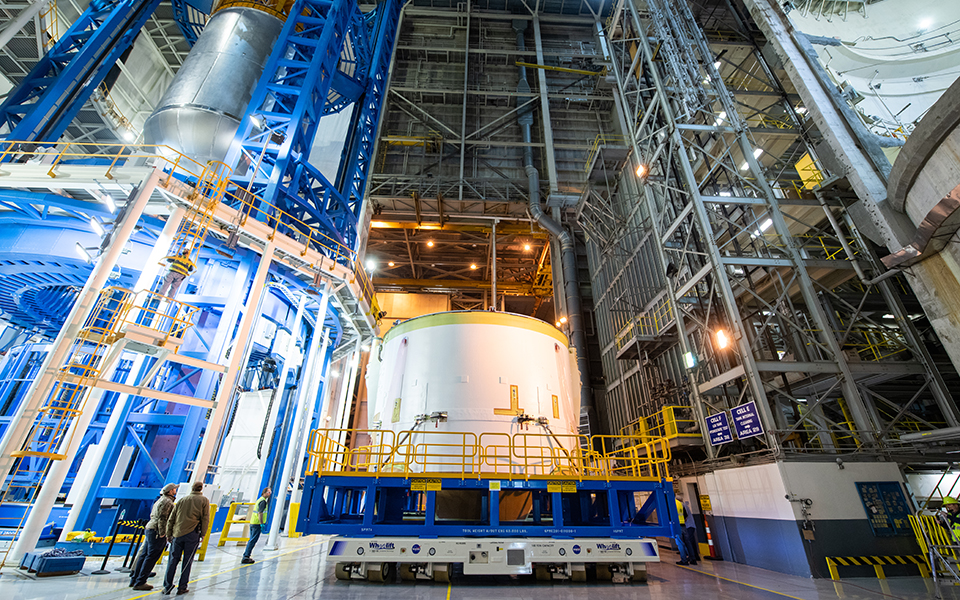
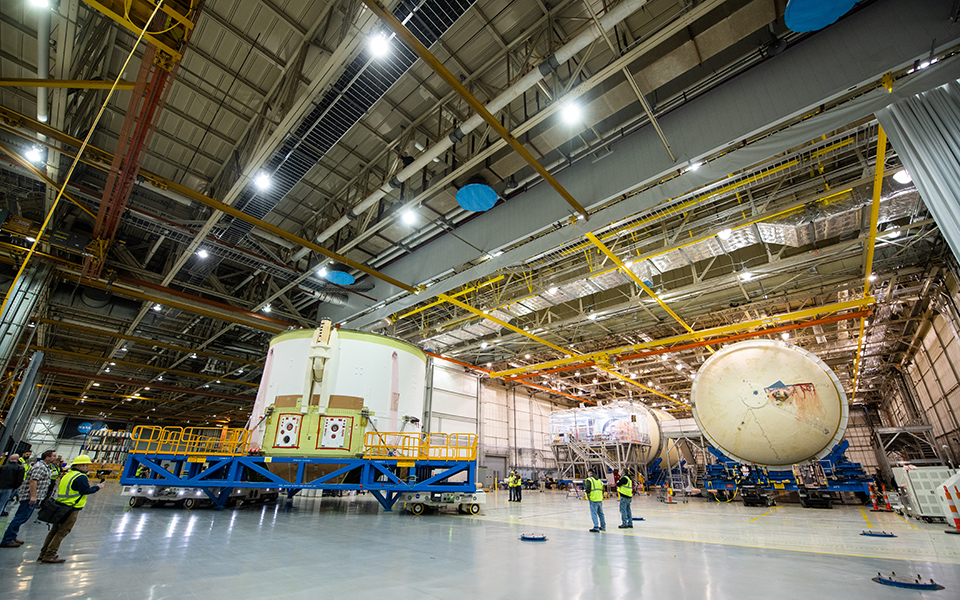
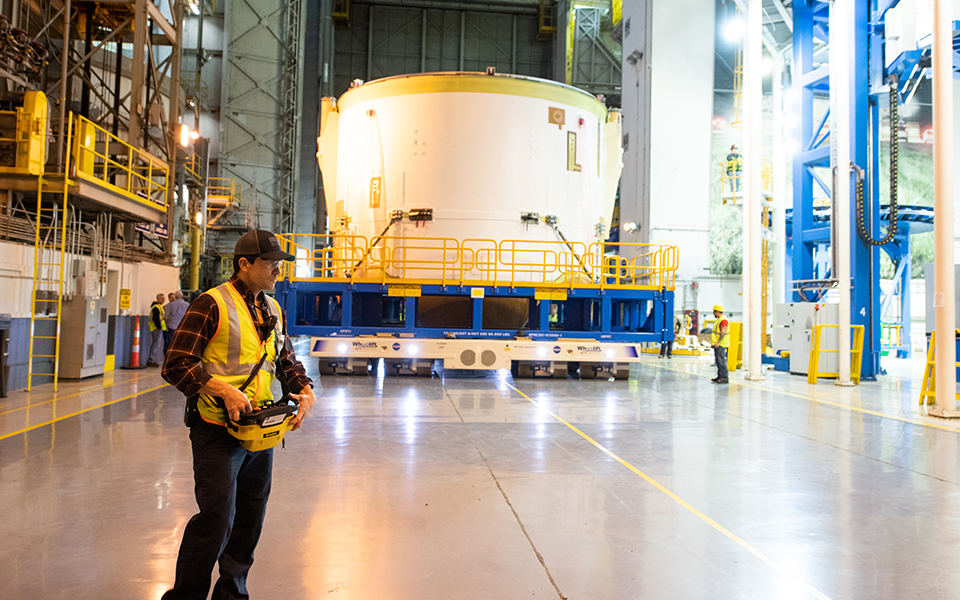
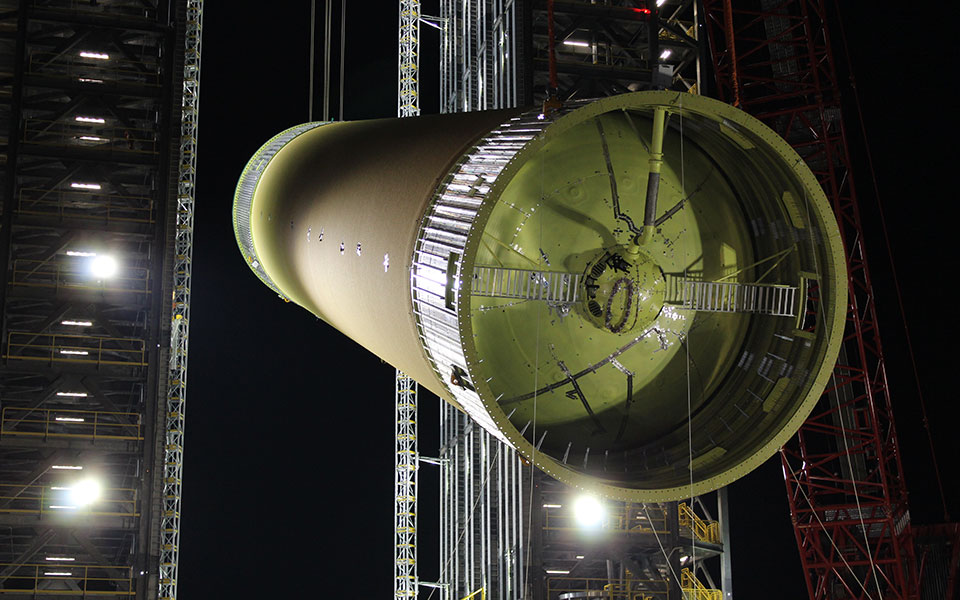
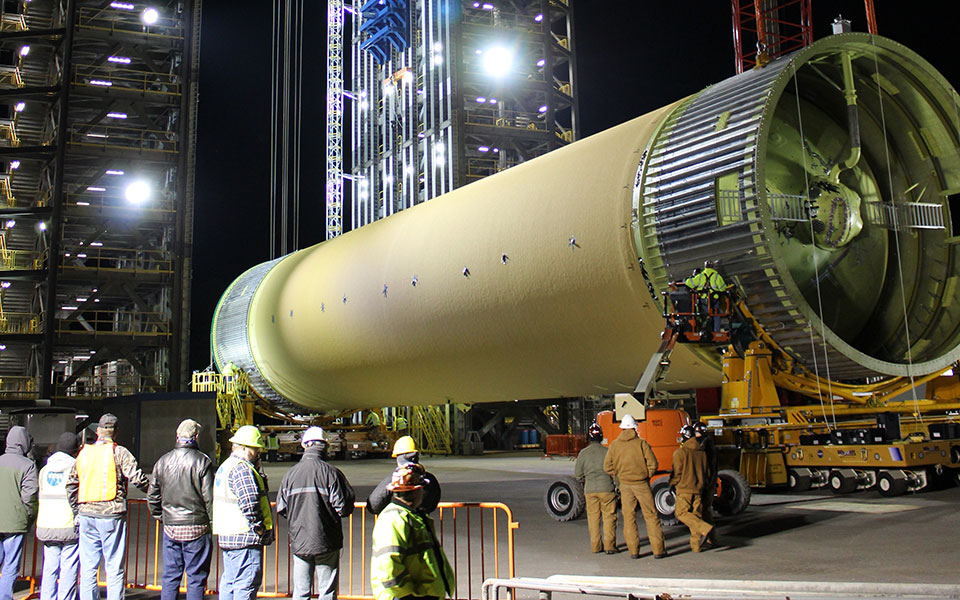
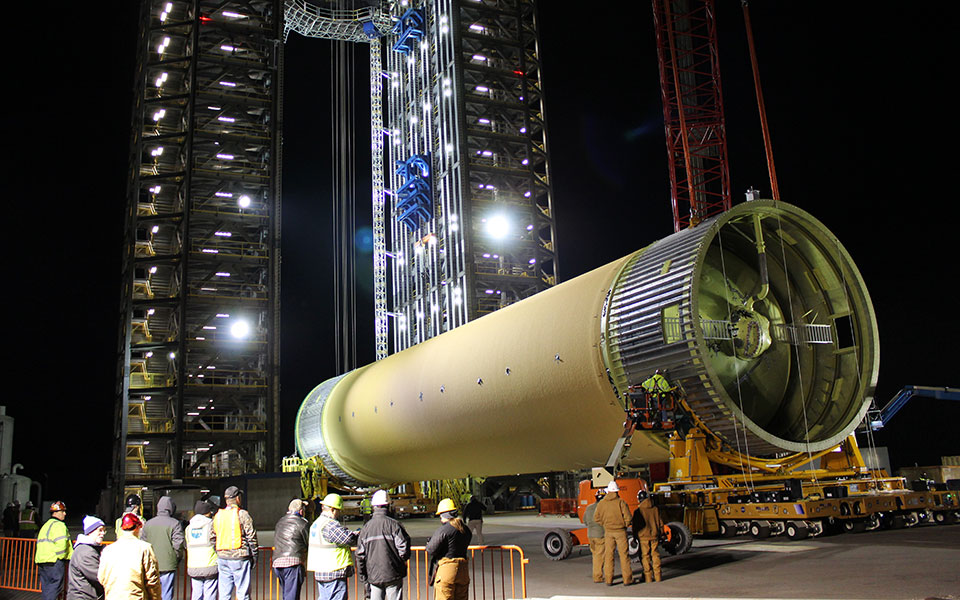
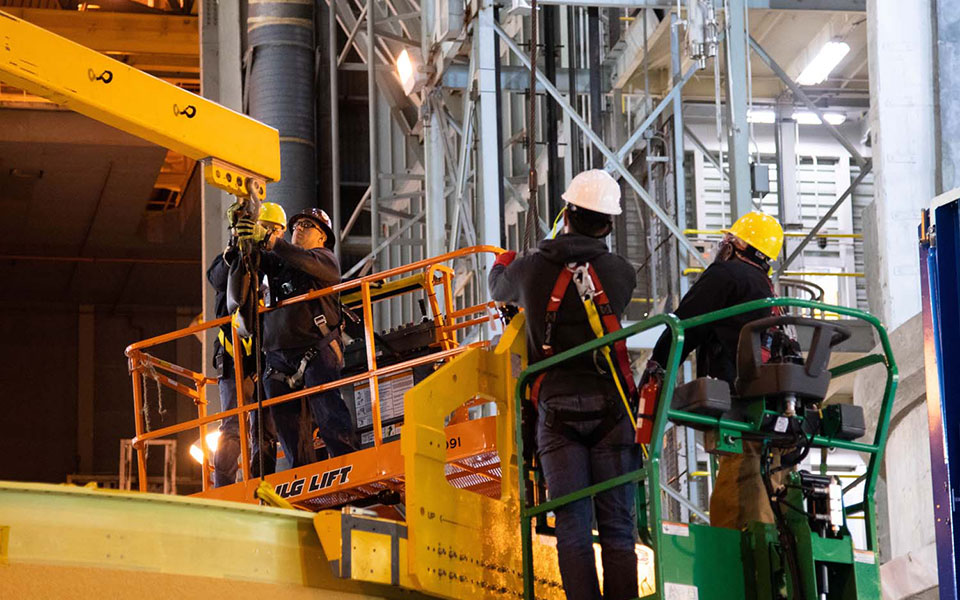
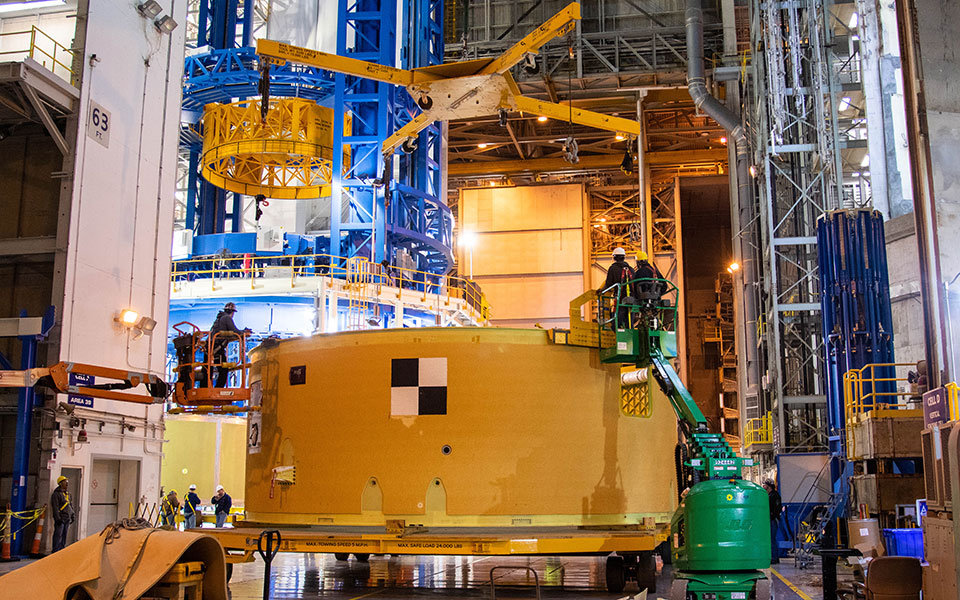
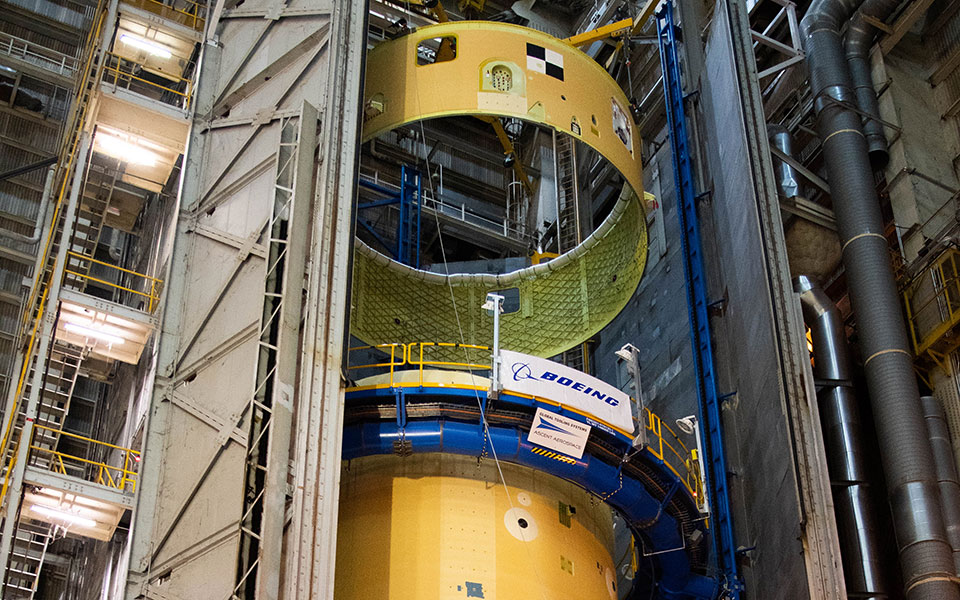
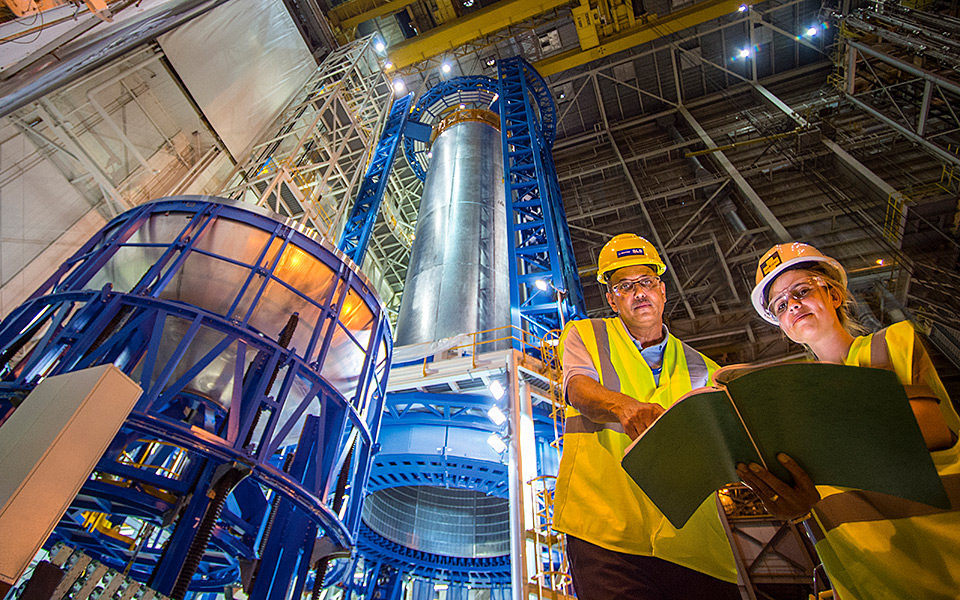
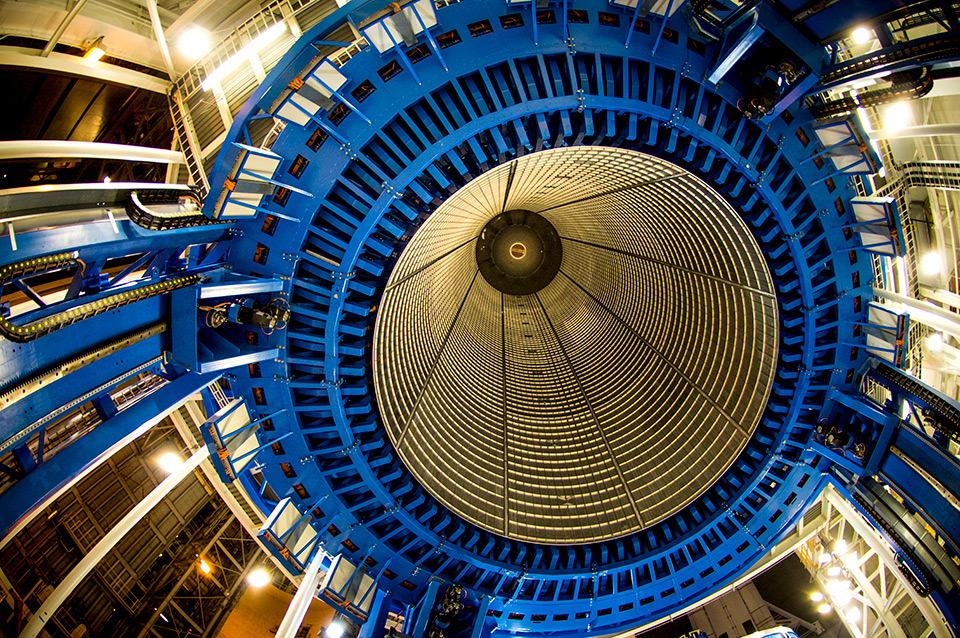
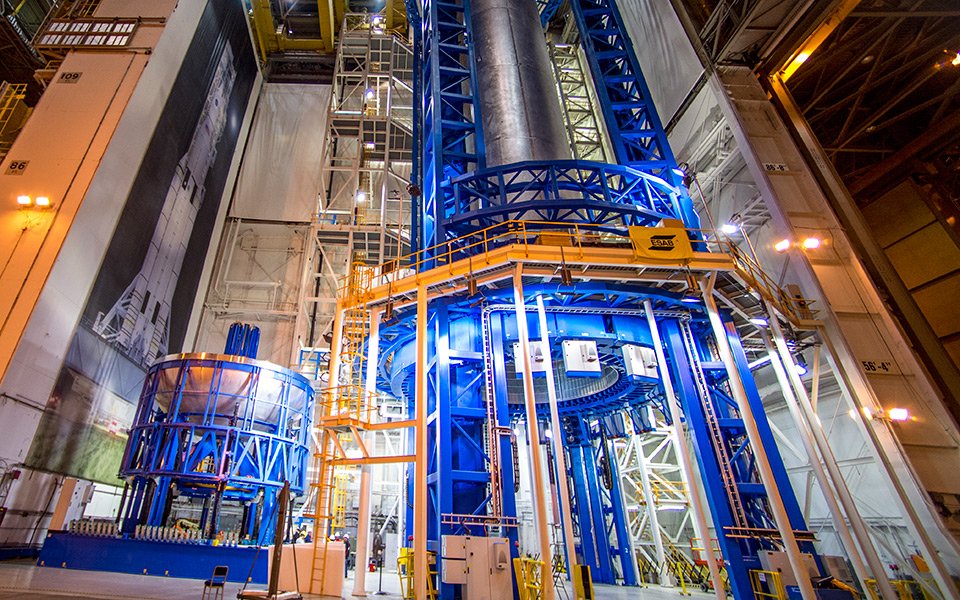
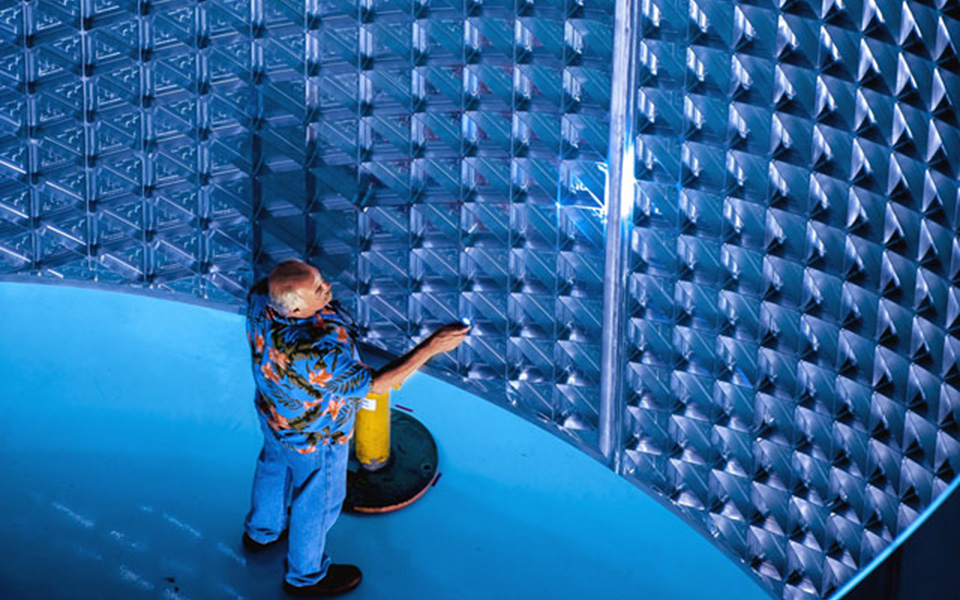
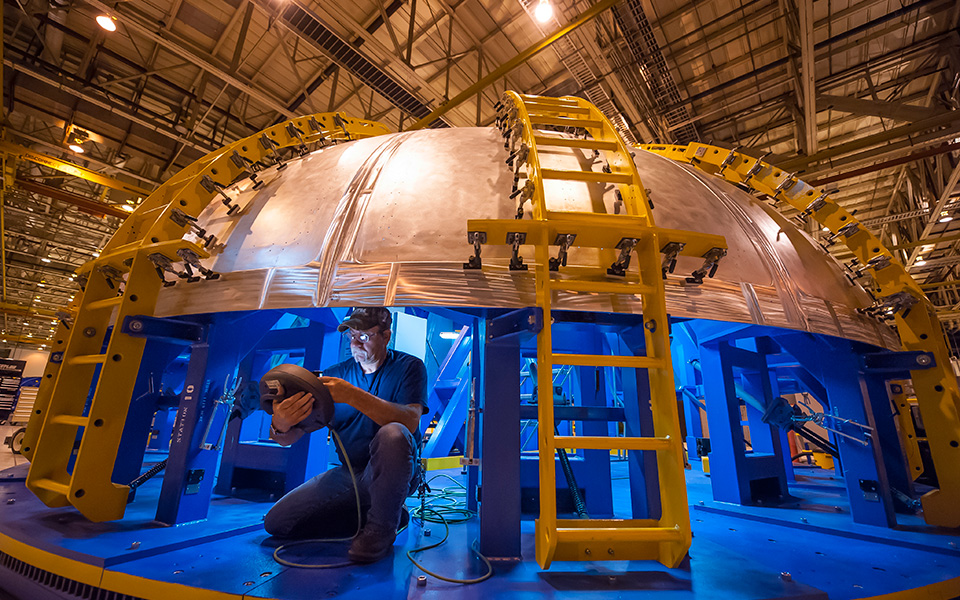
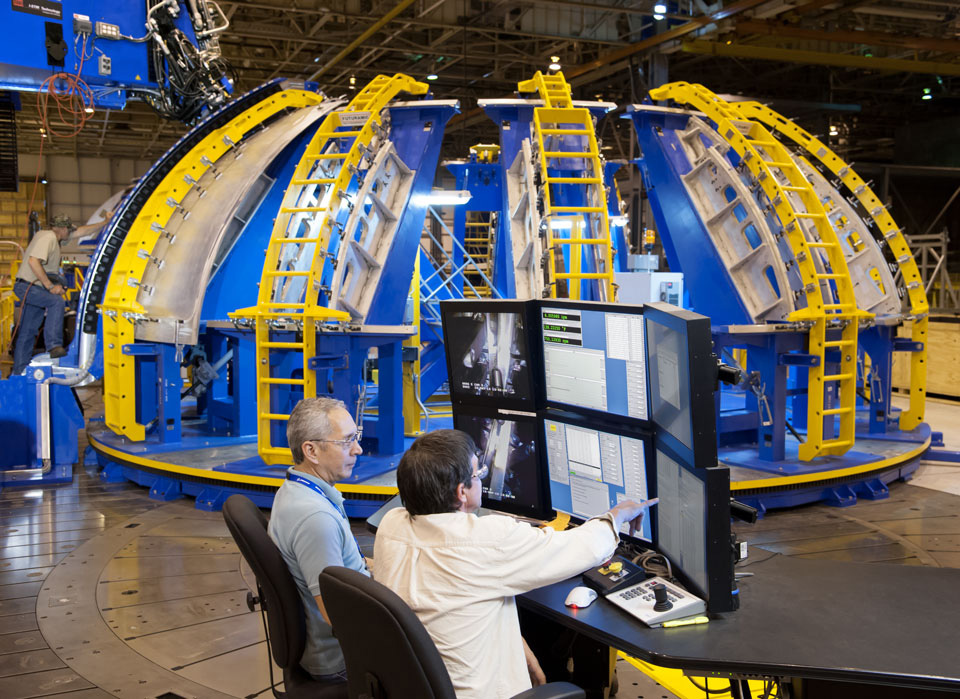
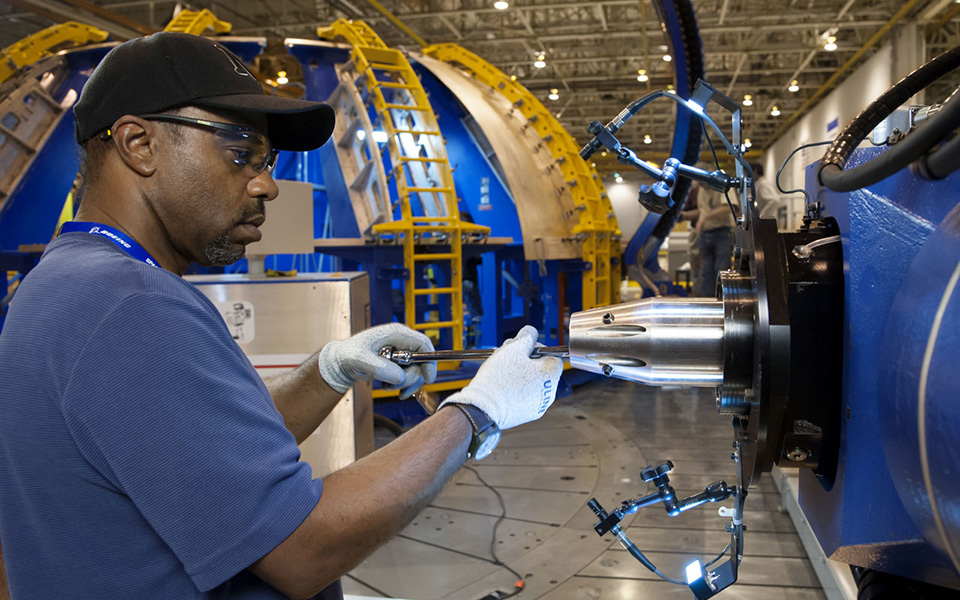
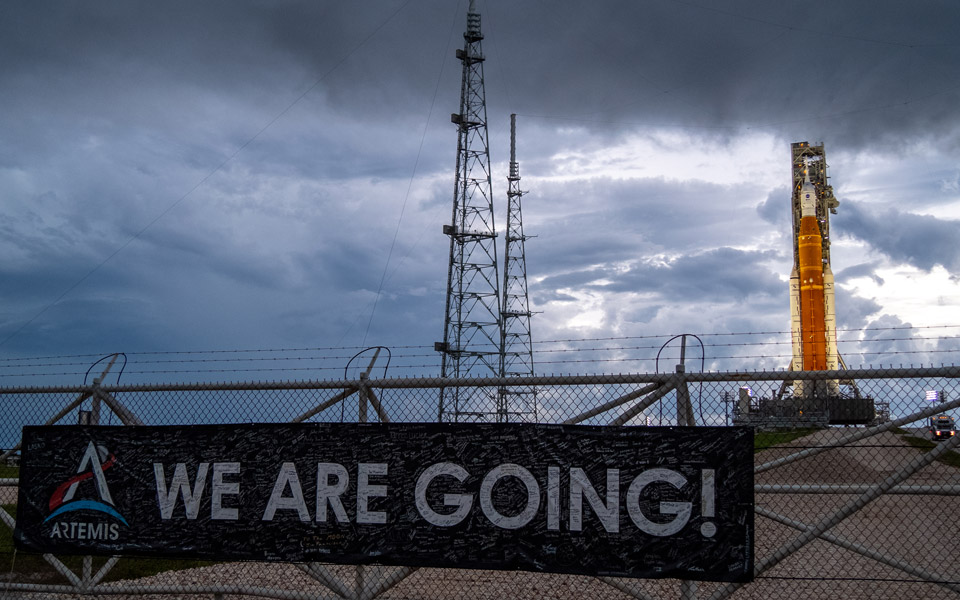
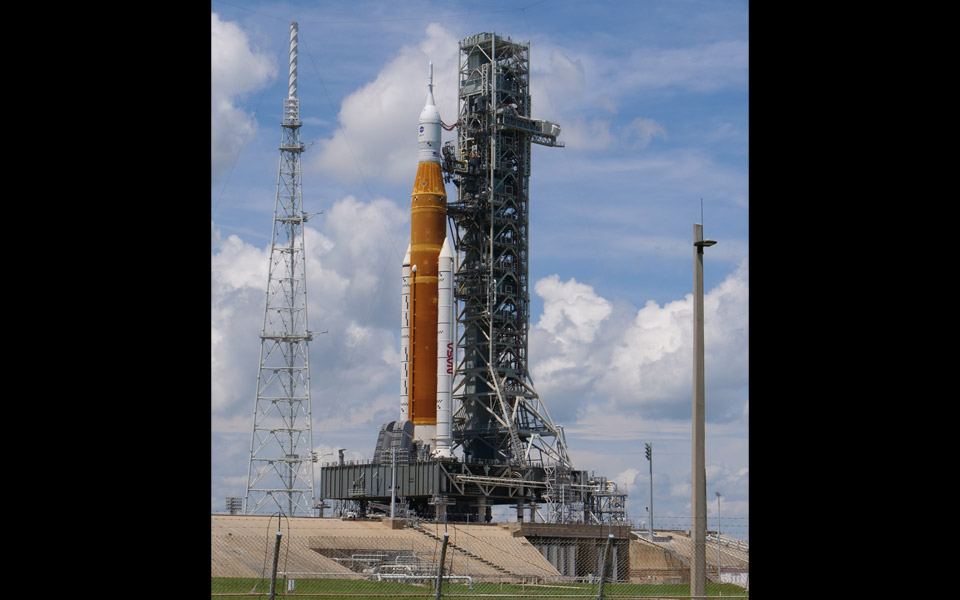

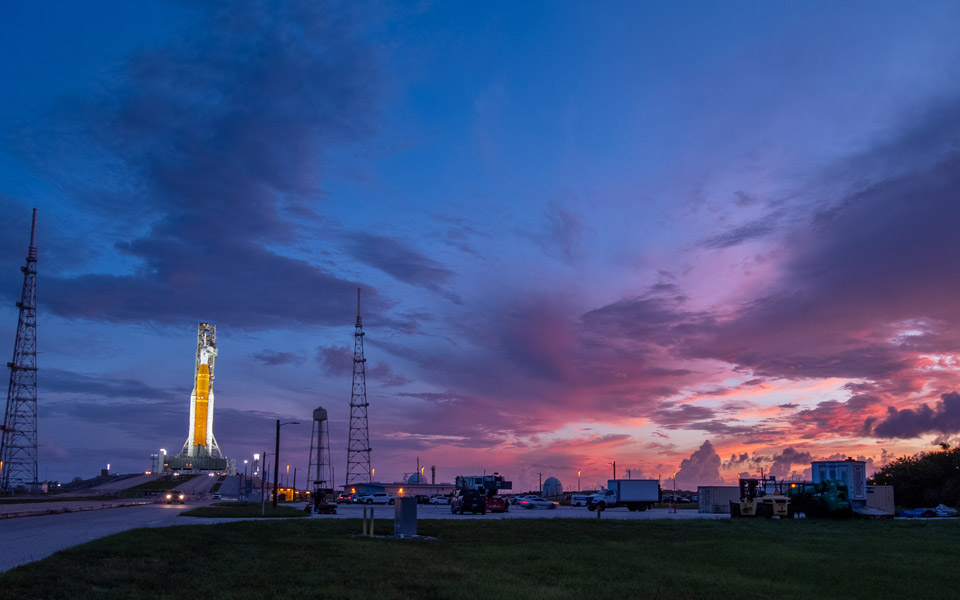
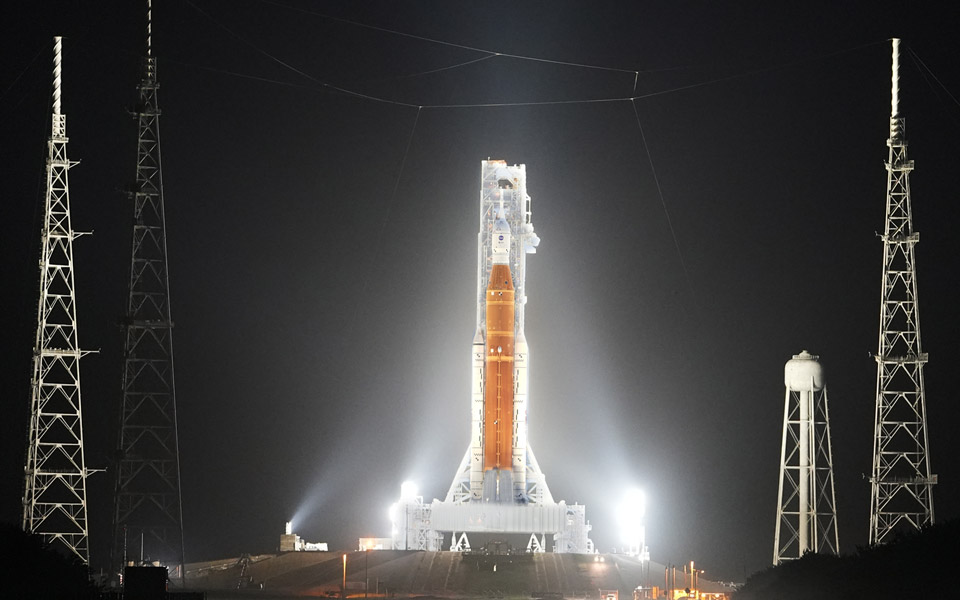
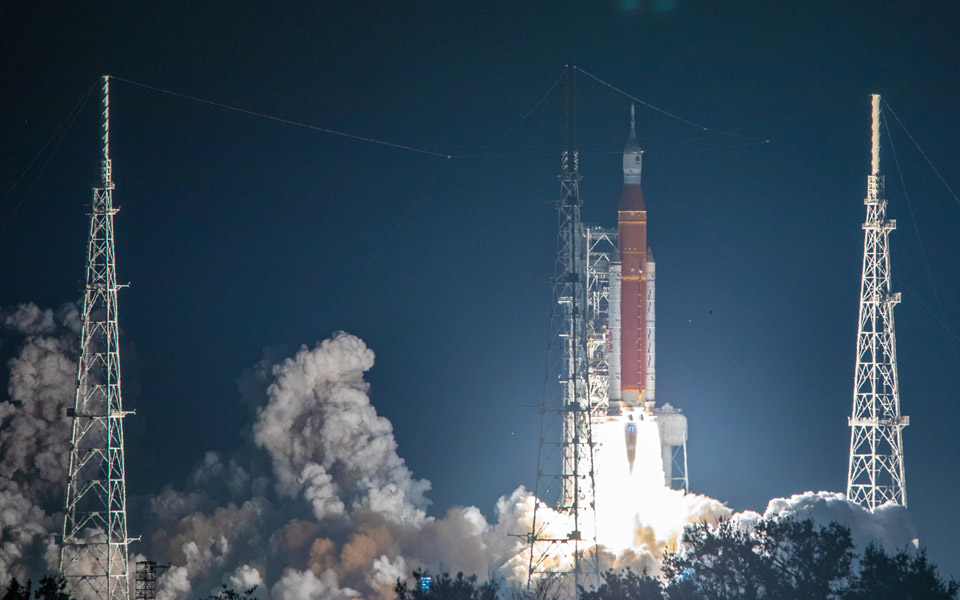
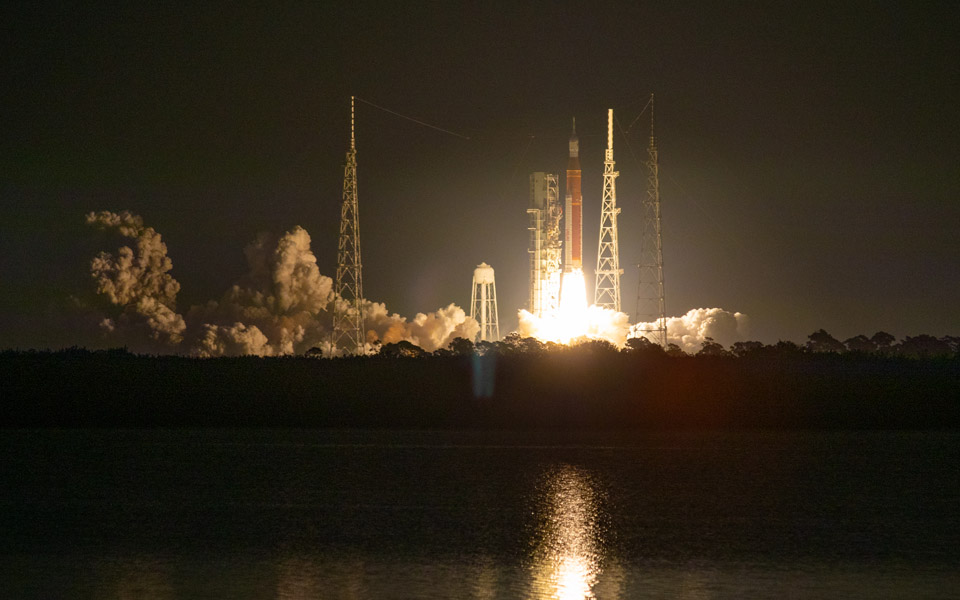
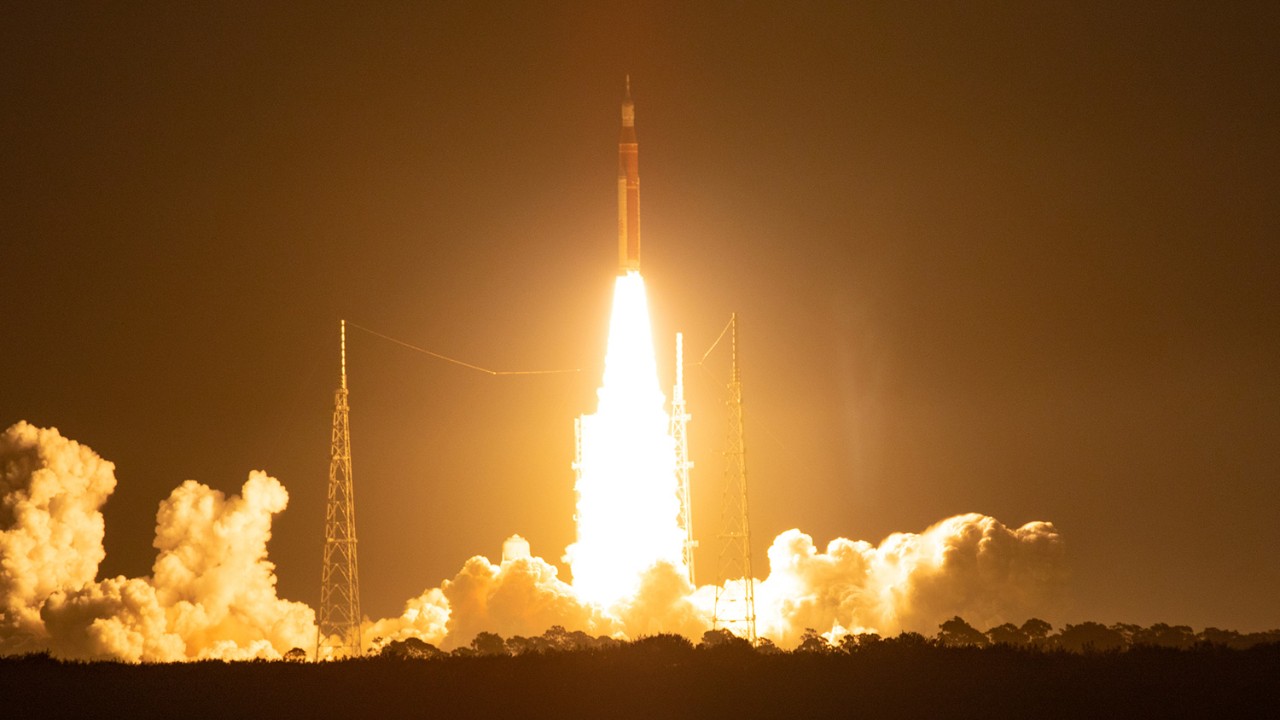
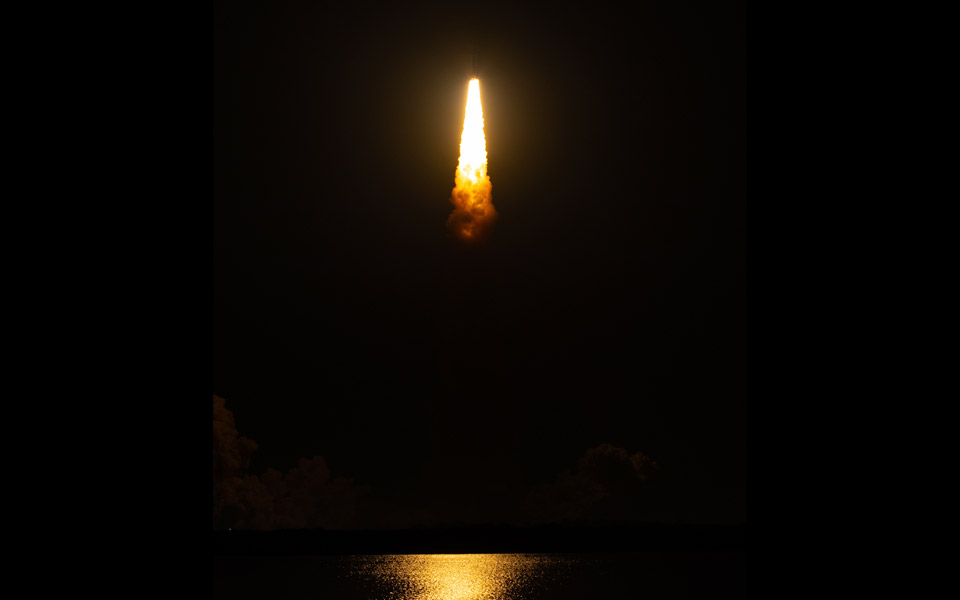
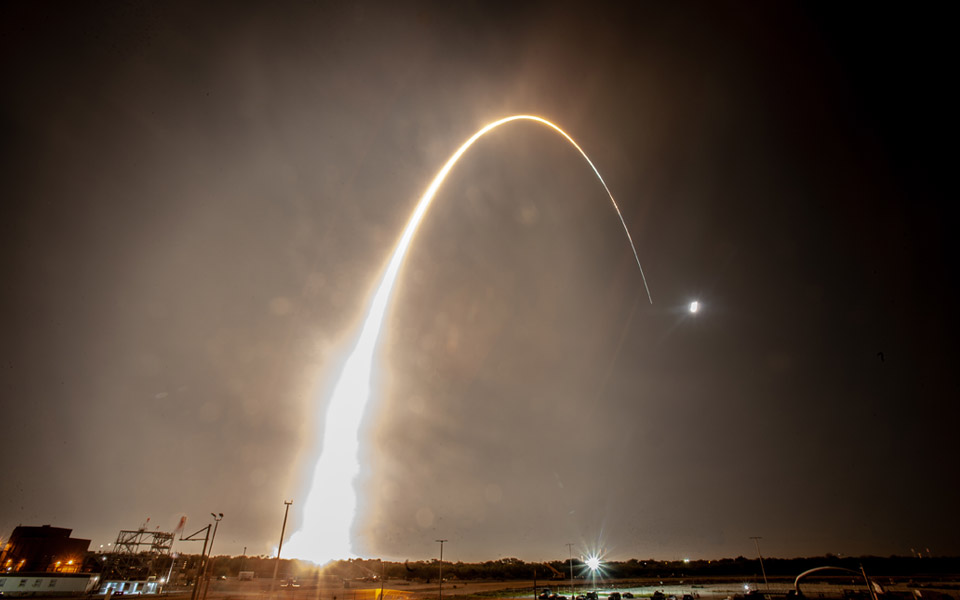
- Image 1
- Image 2
- Image 3
- Image 4
- Image 5
- Image 6
- Image 7
- Image 8
- Image 9
- Image 10
- Image 11
- Image 12
- Image 13
- Image 14
- Image 15
- Image 16
- Image 17
- Image 18
- Image 19
- Image 20
- Image 21
- Image 22
- Image 23
- Image 24
- Image 25
- Image 26
- Image 27
- Image 28
- Image 29
- Image 30
- Image 31
- Image 32
- Image 33
- Image 34
- Image 35
- Image 36
- Image 37
Space Launch System Customer
NASA is Boeing’s customer for the core stage, upper stages and flight avionics of Space Launch System — America’s rocket — which will support the Artemis moon missions and make the next generation of human spaceflight possible.
Boeing is committed to NASA’s Artemis program and to the National Space Council’s vision for continued American leadership and international partnerships in space.
The Space Launch System’s unique capabilities mean that it can perform challenging science, national security, and exploration missions for a broad scope of potential customers. Boeing is not interested in participating in the National Security Space Launch Phase 3 procurement. Boeing remains proud of its role in the SLS program and excited about SLS’s potential.
The Boeing SLS Program is managed out of the company’s Space and Launch division in Huntsville, Alabama, and employs Boeing’s workforce in Huntsville, at NASA’s Michoud Assembly Facility in New Orleans, and at other Boeing sites and with suppliers across the country. The Boeing Exploration Launch Systems office supports NASA on strategy and policy for Space Exploration programs procured by the NASA Marshall Space Flight Center.
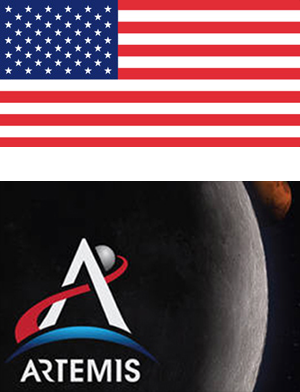